Continuity testing of special foundations permits a quick verification of completed foundations. These tests make it is possible to check even large working areas in a very short time and to verify whether the foundations are continuous and their length corresponds to design assumptions.
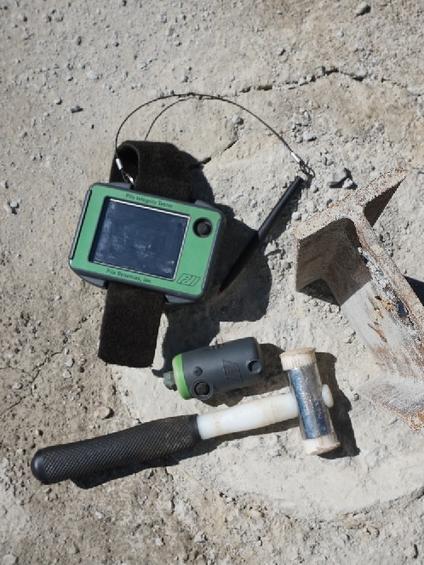
Common uses
Process
Qualitative tests, commonly referred to as "continuity tests", are used for a quick control and confirmation of the quality of completed special foundations, i.e. all types of concrete and reinforced concrete piles and foundation columns as well as diaphragm walls. The commonly used name "continuity testing" does not reflect the true purpose and potential of qualitative tests. Out of the available survey methods used on the market, GEO-Instruments provides its customers with two primary options:
Sonic Echo Method
Sonic Echo Method, or also known as Pile Integrity Tester (PIT), using sound wave propagation in the pile/column core. For the purposes of the test, a low-stress acoustic wave is generated by hitting the pile head lightly several times with a Teflon-head hammer and then recorded with an accelerometer (sensor) placed at the pile head. The acoustic wave traveling along the pile shaft makes it possible to determine whether the length of the completed element is consistent with the design metrics and whether there are no significant constrictions or cracks along the length of the shaft. This method is applied after at least 7-10 days from pile construction on a cut and cleaned upper concrete surface of the pile/column. It is a method used for a rough (approximate) verification of the length and continuity of concrete and reinforced concrete shafts. Due to the simplicity of execution, it allows the technician to check up to approx. 100 elements during a single shift.
CSL (Crosshole Sonic Logging)
CSL (Crosshole Sonic Logging) method which, similarly to the Sonic Echo method, uses acoustic wave propagation in the core of tested elements; however, the wave is induced not by impact but by a special transmitter introduced inside the pile. In order to perform such a test, it is necessary to plan it in advance and prepare special access channels in the form of steel or PVC tubes with an internal diameter of 38-55mm and a length corresponding to the length of the tested element. The number of access channels and their arrangement is designed in advance, and the access tubes themselves are built into the tested element by attaching to the reinforcement or as a self-supporting framework and placed inside the pile prior to or during concreting. Given that the transmitter and receiver have a built-in depth gauge, this method permits verifying with great precision the length of the tested element as well as identifying rather accurately the location and size of any discontinuity or soil inclusion. This method should be applied within 3-7 days from concreting and can be performed from a higher level (prior to excavation) on non-cut heads of piles / columns / diaphragm walls. Due to high work intensity during execution, it is possible to test up to approx. 4-8 piles / columns / diaphragm walls per one working shift (depending on their length).
Advantages
- Quick verification of workmanship quality: Sonic Echo continuity testing method permits a quick and non-invasive verification of virtually all piles executed at the site. While it is not very accurate in identifying potential defects and flaws, it remains an important tool in approximate control of workmanship. Used by an experienced technician, it permits interpreting test results already during site surveys.
- Thorough analysis is possible: with the CSL method, no flaws in the examined piles will be overlooked during the analysis. Thanks to the integrated depth gauge, the actual length of the completed element can be measured with great accuracy. The need for such an analysis occurs in places where piles are few and far between and their workload is significant, which makes each element worth its weight in gold.