Wireless sensors and interfaces provide high precision, low noise measurements, wireless communications and long battery life.
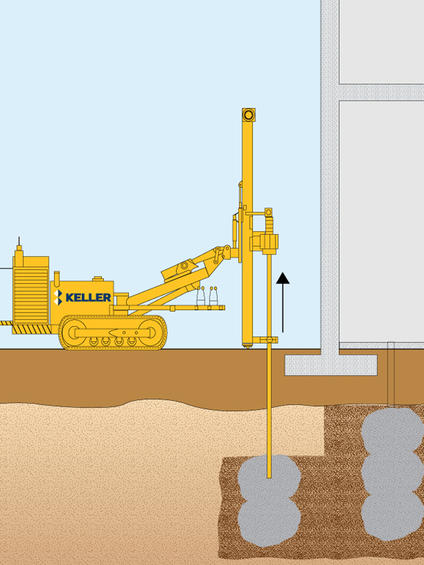
Common uses
Process
Our tilt and laser deformation sensors are all wireless and networked which brings a high degree of flexibility as well as a robust communication link.
The sensors are fully equipped with several MEMS acceleration sensors that output tilt in degrees or mm/m at a high frequency.
The radio transmission protocol for data is proprietary and can handle any convoluted physical environment.
Data processing and communication is handled by proprietary algorithms that provide robust data retrieval, policy distribution, self-diagnosis.
Battery voltage and temperature are also measured internally. This important information can detect unforeseen conditions and plan maintenance reliably.
Gateway units relay information wirelessly and continuously to our web based monitoring interface.
As a result of many years of development on our sensor interface and wireless algorithms, our products’ battery life is extensive, enabling maintenance-free monitoring for up to eight to 10 years depending on the measurement frequency.
At a technical level the system has been tested and proven through 10 years of deployments in highly-demanding environments. And, prior to that, seven years of research at UCL, one of the pre-eminent engineering universities in the world.
The compact sensor can be mounted through drilling, clips, magnets on any structure.
Our gateway comes with a variety of connection options to ensure data is readily available. These include USB connection to a laptop, connectivity via a solar powered
GPRS modem, networking where power is available, and connections to other databases, dataloggers or industrial PCs.
The gateway only needs to communicate with one node for the whole network to send data. This makes deployment very flexible compared to wireless hub and spoke alternatives.
Alternative measurements
Wireless tilts can also include a laser disto to accurately measure the distance from the sensor to a facing surface.
This provides an understanding of the tilt of the structure, as well as absolute displacement.
Other versions of the wireless sensor can include displacement transducers and vibrating wire sensors such as strain gauges or piezometers. This allows a whole range of instrumentation on the same site, all using a unique wireless communication platform, and all reporting to
Advantages
- High accuracy: Sensors and interfaces provide low noise, high precision, digitised measurements with data transmissions every 20 seconds.
- Quick and easy to install: Avoids the issues associated with power, communication, and cabling.
- Flexible and extendable: Wide range of applications, even in which areas where cables can’t be run. The network can be extended over longer distances and wider areas simply by adding more nodes.
- Low maintenance: Battery life for most nodes is eight to 10 years and the sealed, waterproof sensors remain robust and autonomous for years.
- Reliable: The network ensures reliable transmission of measurements without regular maintenance visits. With each node transmitting to its nearest neighbour. If the nearest neighbour fails, the next nearest neighbour forwards the data.
- Robust: Wireless sensors and nodes can operate at temperatures from -40°C to +85°C.
- Easily accessible data: Users can access data via the browser on their PC, tablet and mobile phone.
- Intelligent: We can interact with the nodes and the gateway and visualise and manage key elements remotely. For example, we are able to see and predict battery life on a continuous basis.